The performance of electronic devices continues to improve, but they also consume more power and generate more heat. If heat cannot be dissipated efficiently, the performance of the device will suffer. When electronic components and heat sinks come into contact with each other, there will be air gaps at the solid-solid contact interface. The actual contact area is about 10% of the macroscopic contact area, and a large number of gaps are filled by air. Air is a poor conductor of heat. The thermal conductivity of air at room temperature is only 0.026W/(m·K). The presence of air hinders the heat transfer between the interfaces, causing the interface thermal resistance between the chip and the radiator to increase significantly. Reduce system heat dissipation efficiency, thereby reducing chip life. Poor heat dissipation will reduce the system reliability of electronic products and cause product performance failures. A simple example is when your laptop has poor heat dissipation and may freeze or even be forced to shut down. Poor heat dissipation in a router will frequently cause disconnections and disconnect your network.
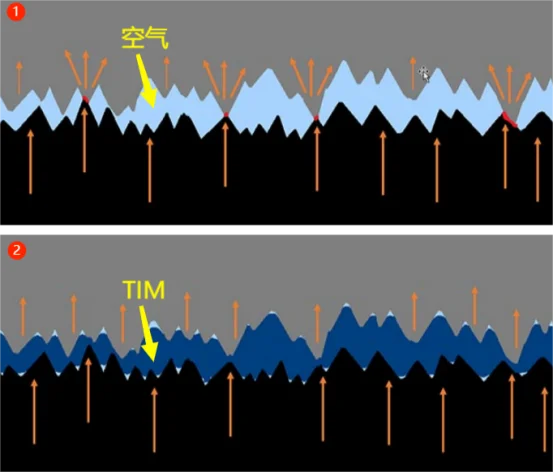
▲Schematic diagram of radiator heat transfer (source: boydcorp.com). The picture above ① does not use TIM, and the heat from the black surface can only be conducted to the gray heat sink at the red highlighted point. The orange arrows help visualize the heat coming from the entire black surface, but there are actually only a fairly few red contact points, with the air pockets represented in light blue. Of course, heat can also be conducted through the light blue air bag, but compared to the level of conduction through the red contact points, it is very inefficient and the amount is very small; the dark blue in the figure ② represents the thermal interface material. Most of the light blue air pockets have been eliminated, replaced by a more conductive soft thermal interface material. TIM can fill the gap between the two surfaces, thereby increasing the effective contact area. Combined with the high thermal conductivity of the thermal interface material itself, it can well solve the problem of unsmooth heat conduction at the material contact interface. In most cases, it is almost impossible to eliminate 100% of the air, so there will still be small pockets of air in the small depressions and holes. However, the thermal performance is now significantly improved compared to the case without TIM; this also applies to any electrical device. Electrical equipment is often sealed in a box, with no thermal interface material conducting heat to a metal heat sink.
In order to ensure the normal operation of the heating element, materials that can quickly and effectively transfer heat are filled between the heating electronic components and the heat dissipation device. This material is called Thermal Interface Materials (TIMs). The use of thermal interface materials essentially changes the thermal path between rough surface solids from conduction through point contact and air to conduction entirely through the solid. Thermal interface materials are considered an essential component of any efficient thermal management system, and these materials are widely used in consumer and industrial electronic systems to ensure efficient heat dissipation and prevent local temperature overloads. Thermal interface materials (TIMs) are a critical component of any thermal management solution.
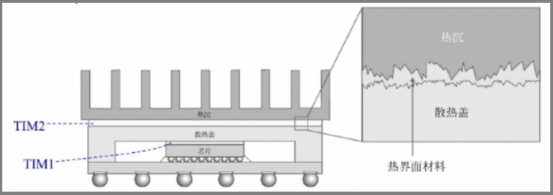
▲According to the application of TIM in advanced packaging, it is divided into TIM1 and TIM2 according to its location. TIM1 is also called first-level TIM. It is the thermal interface material between the chip and the package shell. It is in direct contact with the chip that generates great heat. It requires TIM1 material has low thermal resistance and high thermal conductivity, and the CTE is matched to the silicon wafer. TIM2, also known as secondary TIM, is the TIM between the package shell and the heat sink. TIM2 has lower requirements than TIM1. TIM1 needs to have electrical insulation properties to prevent short circuits in electronic components, and is generally made of polymer-based composite materials; TIM2 does not have electrical insulation performance requirements, and is generally carbon-based TIM.
The thermal conductivity of polymers without thermal fillers (resin materials: silicone, epoxy resin, polyurethane, acrylic) is about 0.1W/(m·K). Simply replacing air with grease can still reduce the thermal resistance by about five times [ The thermal conductivity of air is only 0.026W/(m·K)]. At present, almost all thermal interface materials are filled with thermally conductive filler particles. The addition of thermally conductive fillers improves the thermal conductivity of the polymer, while retaining the polymer’s advantages of good flexibility, low cost, and easy processing and molding. Through the addition of fillers, The thermal conductivity of polymer (resin material) can be increased to the range of 7W/(m·K). Common thermal conductive materials include metal fillers (especially silver) and inorganic particle fillers: alumina, magnesium oxide, silicon oxide, aluminum nitride, boron nitride and diamond powder, etc.
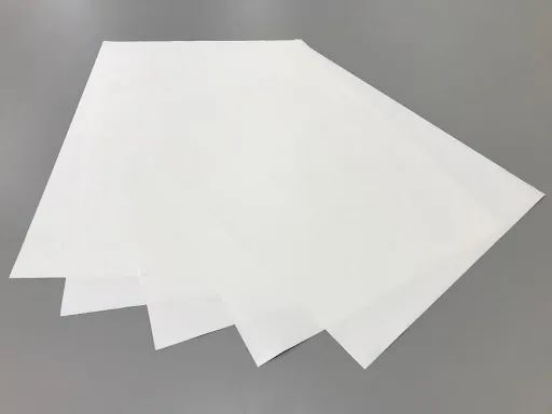
▲ Shin-Etsu Chemical’s “TC-BGI series” heat-dissipating silicone rubber sheet thermal interface material for electric vehicle parts has a high thermal conductivity of 7W/(m·K), and a 0.3mm thick sheet can guarantee a withstand voltage of 5kV. According to Shin-Etsu Chemical’s official website, TC heat-dissipating silicone rubber sheets contain a high proportion of thermally conductive fillers, use boron nitride compounds with high thermal conductivity as fillers, and are reinforced with glass cloth to have excellent tear strength.
According to the needs of actual application design and production process, thermal interface materials will appear in different product forms. What are the characteristics of different thermal interface materials?
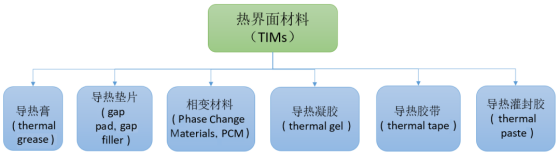
I.Common thermal interface material products
▼Thermal conductive medium performance index table
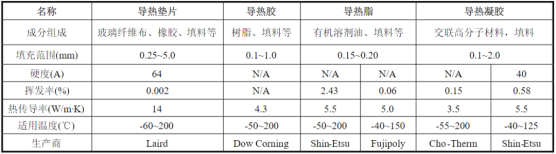
1.Thermal paste/thermal grease
It is in liquid or paste form and has certain fluidity. Under a certain pressure (100~400Pa), it can form a very thin film between two solid surfaces, which can greatly reduce the thermal resistance between heterogeneous surfaces. It mainly uses polymer materials such as silicone or hydrocarbon oil as the matrix, and uses various thermal conductive materials as fillers: AlN or ZnO. You can also choose BN, Al2O3, SiC or silver, graphite, aluminum powder and diamond powder. The thermal paste process is simple and the construction method is usually screen printing or direct application. It does not require curing and the cost is low. It has the largest market share and high thermal conductivity; it requires very little fastening pressure during use; it has good wettability with the base material, which is conducive to air discharge and improves the overall thermal conductivity. Most thermal pastes are silicone-based (thermal grease), and there are silicone-free greases on the market for silicone-sensitive applications. For sensitive applications where the use of silicone grease is prohibited, such as in optical components and automotive lighting, silicone-free products are available.
The disadvantages are: it is fluid, easy to overflow and contaminate-Pump-Out, and is not easy to clean, and has poor user affinity; the base material is prone to separation after multiple cycles, oil spillage occurs, and it is easy to dry out over time.
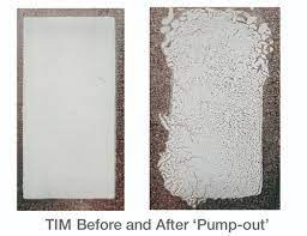
2、Thermal pad
Thermal conductive silicone sheets, thermally conductive silicone pads, electrically insulating thermal conductive sheets or soft heat dissipation pads are usually sheet-like thermal interface materials that use silicone rubber as a polymer matrix and add high thermal conductivity fillers. It is mainly used to fill the gap between heating components and heat sinks or metal bases to complete heat transfer between the two, while also serving as shock absorption, insulation, and sealing.

▲Thermal pads are naturally sticky on one or both sides
The matrix is mainly made of silicone polymer, which has relatively stable dielectric properties at high temperatures, is resistant to oxidation, has good insulation, is water-resistant and flame-retardant, and is easy to process. The fillers are mostly nitrides AlN, BN, or metal oxides ZnO, Al2O3. The filling amount and ratio will affect the thermal conductivity of the thermal pad. If the insulation requirements are not high, you can add more high thermal conductivity and non-insulating fillers to obtain higher thermal conductivity.
Thermal pads are usually used in places where it is inconvenient to apply thermal paste. For example, the power supply part of the motherboard version has a relatively large current part, but the mos tube part is not flat, and it is inconvenient to apply thermal paste. Therefore, thermal pads can be attached. In addition, under the radiator of the graphics card, multiple components need to be in contact with different parts of the graphics card, and thermal paste is inconvenient to use. You can use thermal pads instead. Thermal paste with the same thermal conductivity is better than thermal pad because the thermal resistance of thermal paste is very small. Therefore, in order to obtain the same thermal conductivity, the thermal conductivity of the thermal pad must be higher than that of the thermal paste.
3、thermal gel
Thermal conductive gel is a commonly used thermal interface material that has the advantages of thermal conductive pads and thermal conductive paste: Thermal conductive gel is in a paste form when used, has good fluidity, and can fill in gaps under relatively small installation pressure (less than 20 psi). The gap between two flat solid surfaces; it can be gradually vulcanized after assembly, so the assembly thickness can be very low (lower thickness than thermal pad compression), the thermal resistance is relatively low, and it can also be designed to have higher Thixotropy, so that it does not flow obviously when compressed and maintains a certain shape. Compared with thermal paste, it can also fill larger gaps. It is stable after vulcanization and has no risk of oil and drying. It is said that a good thermal gel can have a service life of up to 10 years, but it is normal for thermal grease to be scrapped in one year and need to be reapplied.
4、Thermal conductive phase change materials
Phase change materials have an energy buffering effect. Through heat absorption or release during the phase change process, additional heat dissipation paths are added, which is conducive to the propagation and diffusion of waste heat, prevents the temperature from rising sharply, and alleviates the operating temperature of components, thereby extending the service life. Typically, phase change materials are silicone-free paraffin wax materials, but they can also be acrylic-based.
The total thermal conductivity of the phase change material and its carrier material depends on the thermal conductivity of the carrier material. According to different carrier materials, phase change materials are divided into the following two categories:
1) Organic phase change materials, or polymer phase change materials. With a melting temperature of 50~80°C, thermoplastic resins, such as paraffin, esters, and alcohol organic compounds, have the advantages of stable performance and low cost. The polymer matrix has poor thermal conductivity and needs to be added with high thermal conductivity materials. The wettability is not as good as that of thermal paste, and it cannot effectively fill the interface gaps after multiple cycles.
2) Inorganic phase change materials mainly include alloys and molten salts. The metal itself (such as Al) has high thermal conductivity and does not require the addition of thermal conductive materials. However, it is easily oxidized and corroded and has poor ability to fill interface gaps.
- Thermal conductive tape
Thermal tape creates a strong bond between components and heat sinks without the need for additional fasteners, reducing the need for screws and clamps. Thermal conductive tape is used as a bonding material for heat dissipation components. It has high thermal conductivity, insulation, and fixation functions. It is also soft, conformable, and strongly adhesive. Thermal conductive tape is roughly the same as ordinary tape or double-sided tape. It is a tape that is coated with thermal conductive adhesive on one or both sides of a supporting material such as polyimide film or metal foil tape. Compared with other liquid conductive pastes, it simplifies the process, can adapt to the irregular shape of the contact surface, will not overflow and contaminate components, has good stability, and will not move easily.
Thermal conductive tape is filled with limited thermal conductive particles and has a relatively low thermal conductivity, usually 1~2W/(m·K). It is only used for bonding and is more suitable for low-power components.
- Thermal conductive potting glue
Potting refers to the packaging operations of properly assembling, bonding, isolating and protecting the various components of electronic components as required. It can protect against dust, moisture, and shock, and can extend the service life of electronic components.
Thermal conductive potting glue is mostly two-component glue and can be cured. Strictly speaking, potting glue is not an interface material because it fills the entire module space. The potting glue is liquid before solidification and has fluidity. The viscosity of the glue varies according to the material, performance and production process of the product. The potting glue can only realize its use value after it is completely cured.
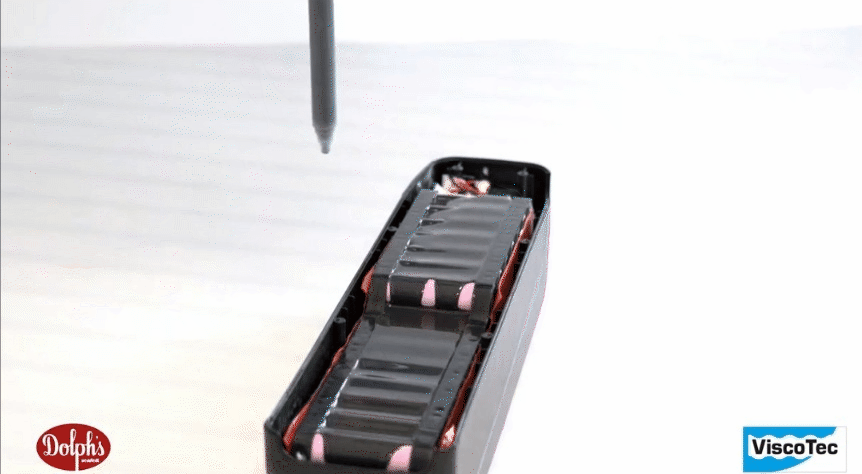
Thermal conductive potting glue is formed by adding thermal conductive fillers to ordinary potting glue, such as SiO2, Al2O3, AlN, BN, etc. Different thermal conductive fillers can obtain different thermal conductivities, and ordinary ones can reach 0.6~2.0W/( m·K), high thermal conductivity can reach 4.0W/(m·K).
II.Thermal conduction application cases
- Battery pack
As battery technology continues to be upgraded to increase energy density, thermal management capabilities during charging and discharging processes are critical to optimizing performance. Compatibility and process customization for different battery types are key elements. Cylindrical batteries usually require adhesive or potting compound. Pouch batteries often use caulking. Square batteries can use three types of adhesives: adhesive, potting glue or caulking agent.
- Charger
Encapsulants and caulks improve heat flow in inductors and transformers, optimizing performance during charging and increasing product life. The low-viscosity encapsulant easily flows into fine crevices and fully impregnates irregularly shaped magnetic components, helping to displace air and reduce inductor noise. Using pre-filled components, caulk can even create a thermal interface between the component and the thermal substrate.
- Motor
Heat causes the motor to lose power and shorten its service life. Thermal conductive epoxy and silicone potting and encapsulants help manage heat, increase power density, and extend motor life.
- Power electronic devices
To extend the service life of power electronics, the thermal resistance needs to be kept low and components protected from shock, moisture and debris. Low viscosity, high thermal conductivity potting and encapsulants provide a robust thermal interface and protect delicate electronic components. Other thermal interface materials – gels, silicones, adhesives and caulk – not only improve heat dissipation, but also provide excellent insulation and vibration damping.